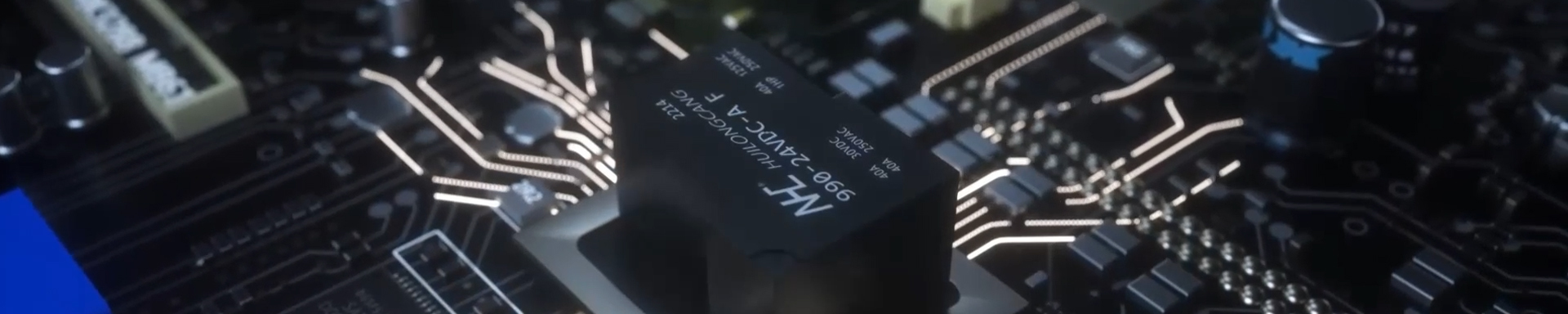
Reaction characteristics of power control relays 02
2022-09-21 15:23In the power control relay the return spring and the contact spring are made of circular or sheet-like elastic materials (such as spring steel wire, tin bronze, phosphor bronze, brass, German silver, silver magnesium nickel, etc.). When it is mechanically deformed, it has a certain elasticity. We all have this feeling in practice, the greater the deformation of these springs, the greater the elastic force it produces: the smaller the deformation, the smaller the elastic force; no deformation, that is, the spring is in a free state, and no elastic force is generated. Further experiments and theoretical analysis show that: within a certain range, the size of the elastic force (F) is proportional to the size of the deformation (X). Mathematically expressed as: F=CX
It is represented by a curve, as shown in Figure 2-9. Here the proportionality factor O is a constant that reflects how "soft" a certain spring is. Because, if the two springs produce the same size change, the spring with a large C will produce a large elastic force. So, O is called the "stiffness" of the spring. Its size is determined by the properties of the spring material and the geometric size of the spring. Knowing the relationship between the elastic force of the spring and its deformation, it can be used to analyze the various reaction force characteristics of the power control relay. Here is an example to illustrate. Figure 2-10a shows a schematic diagram of the armature and contact parts of a small power control relay. All the reaction forces are generated by four reeds: return reed ④, moving reed ③, static reed ① and ②. Since the armature is rotating, the distances from the action points of each reaction force from the shaft are different, and their effect on the armature is also different. Therefore, in order to be able to compare with the suction, these forces must be converted to the suction point A according to the leverage ratio. Similarly, the overtravel and opening distance of the contacts also need to be converted into the length of the air gap at A. After these treatments, we can analyze the forces generated by various reeds according to the different positions of the armature.
(1) Within the distance from δm to δ3: when the armature is in the open position (the air gap is δm), the return reed ④ generates a reaction force F4 due to the previous deformation. When the armature starts to move from the open position and the air gap is reduced, the return reed will continue to deform, and the generated reaction force will increase according to the law of formula (2-1). When the air gap δ=δ3, the reaction force increases to F3. In this distance, the reaction force acting on the armature is only generated by the return reed, and the reaction force characteristic is 4~3 sections of the curve. This distance is called the free travel of the armature. With it, a buffer zone can be given to the armature to bounce back due to collision or external vibration when the armature is in the open position, which is beneficial to improve the reliability of the contact work.
(2) Within the distance from δ3 to δ2: when δ=δ3, the push rod begins to contact the moving reed ③, and the static reed ② also begins to act on the armature. Therefore, the reaction force will be determined by the return reed ④, the moving reed ③ and the static reed ②. Obviously, the force of the moving reed is against the closing of the armature, while the force of the static reed ② indirectly helps the armature to close. And because their interaction forces are equal, the reaction force acting on the armature at this moment (δ3) is still F3. When δ3 begins to decrease, the force of the static reed ② decreases and the force of the moving reed increases, and the force acting on the armature is the 3~2 segment of the curve. When δ=δ2, the force of the reed ② becomes zero (in a free state), and the normally closed contacts begin to separate.
(3) Within the distance from δ2 to δ1: At this time, the force acting on the armature is only determined by the moving reed ③ and the return reed ④, which is the 2~1 segment of the curve.
(4) Within the distance from δ1 to δ0: corresponding to δ1 is the position where the moving reed ③ and the static reed ① have just started to contact, and δ0 is the minimum air gap value that exists between the armature and the static iron core after they are finally closed. . Within this distance, the total reaction force is determined by the above two reeds and the return reed, which is segment 1~0 of the curve.
In this way, the total reaction force characteristic of the power control relay is obtained, as shown by the broken line in the figure. Among them: F1 is the conversion value of the final pressure of the normally closed contact; respectively is the conversion value of the overtravel, opening distance and final pressure of the normally open contact. From the above analysis, it can be known that the characteristics of the reaction force have the following characteristics:
(1) The reaction force characteristic is a polyline composed of straight line segments with different slopes, and each polyline segment represents different working stages of the armature and the contact.
(2) The main parameters of the contact (overtravel, distance, initial pressure, final pressure, etc.) are reflected in the reaction force characteristic curve.
(3) If the power control relay adopts the contact reed, the initial pressure of the contact is equal to zero, and the reaction force characteristic curve will be a continuous broken line. If there is initial contact pressure on the contact spring surface, the reaction force characteristic will have a sudden change at the position where the normally closed contact is just separated or the normally open contact is just closed. It can be known after analyzing the reaction force characteristics of the DC contactor shown in Figure 1-4).
(4) By changing the pre-pressure or stiffness of the return reed, the maximum stroke of the armature, the parameters of the contact, etc., the reaction force characteristics can be changed, thereby changing its effect on the opening and closing movement of the power control relay. This will be mentioned later.
related information:Reaction characteristics of power control relays 01